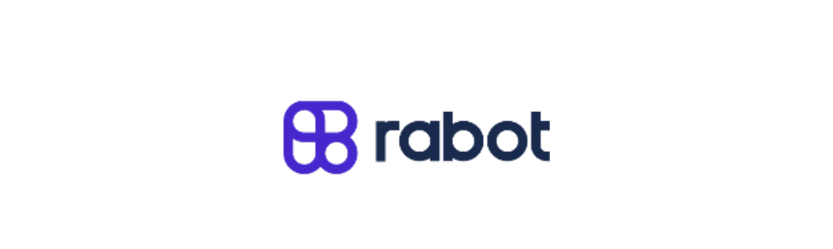
HOW RABOT REVOLUTIONIZED PACKAGING QUALITY CONTROL OPERATIONS FOR STACI USA
KEY RESULTS
Reduction
In quality assurance and customer support costs, improving client trust
Visibility
Into packaging operations with video available for every order packed at Rabot-powered packing stations
Increase
In productivity by identifying process inefficiencies quickly, and introducing enhancement to protocols
.png?width=2048&height=998&name=33%20(1).png)
AIMING FOR PERFECT ORDER FULFILLMENT USING AUTOMATED PACKAGING SYSTEMS
Staci USA’s reputation in the supply chain industry speaks for itself. It’s no secret that Staci is a leader in its space; the company consistently processes order fulfillment with accuracy in the 99th percentile—99.5% at the time they began talking with Rabot, in fact, which exceeds the industry average. The company processes more than 25,000 daily orders at its headquarter fulfillment center that serves 10+ major lifestyle and beauty brands. Even more impressive is the fact that Staci maintains such a high level of accuracy with tremendous packaging complexity: each brand in its headquarters center has a unique protocol for packing orders as well as multiple supervisors and team leads who oversee a single client’s fulfillment operations.
SETTING THE STAGE: TECHNOLOGY SOLUTIONS FOR INTELLIGENT PACKAGING
While Staci’s impressive 99.5% order fulfillment accuracy is above the industry standard, it is Staci’s mission to drive toward 100% accuracy. Prior to employing the Rabot Pack solution, Staci measured its fulfillment accuracy manually. This quality assurance process involved randomly selecting and opening packed orders and checking it against the bill of materials, evaluating the dunnage, and then repackaging them and sending them out. This process cost Staci 10% of its operational costs in the warehouse. While this method of quality control gave decent insight into overall quality of packaging accuracy, the lack of visibility video coverage on the packing lines failed to explain why any errors may have occurred.
.png?width=1867&height=1400&name=rabots2%20(1).png)
THE PROBLEM
Manual quality assurance methods also only catch errors after they have occurred, and do not have the ability to catch and correct any error in real time. Stakeholders at Staci wanted to ensure that they were optimizing their packing operations continuously and proactively for all their clients in order to tackle the growing order volumes. Staci needed a scalable solution to identify and eliminate issues as they occur, and wanted to remove non-value-add steps to its packaging processes—and they needed it done quickly.
THE SOLUTION
Rabot’s Automated, Real-Time Packaging Solution Delivered:
Instant Visibility
Into packing operations, and the ability to correct errors before they become costly to fix and/or reach the end user.
Accurate System
A system for accurately and quickly measuring baseline performance on the fulfillment floor to drive better performance and design more streamlined protocols
Collaborative Tools
Seamless collaborative tools for teams that improve employee engagement and communication between operations, management, and client engagement teams
Scale Fulfillment
A way to scale fulfillment processes with a much higher rate of accurate orders packed
SCALING TO MEET THE EXPLOSION OF ECOMMERCE PACKAGING
The minutes and hours in a workday to fulfill orders is finite—there is only so much time in a day to identify and correct packing errors. With manual quality assurance processes, much of that time is spent identifying that an error in the packaging process happened at all. In Staci’s case, data and reporting was tracked using manual spreadsheet entries, but the time this took wasn’t quick enough to make real-time improvements on the warehouse floor. Instead, time was spent responding reactively to problems rather than proactively improving processes to prevent these errors from ever occurring.
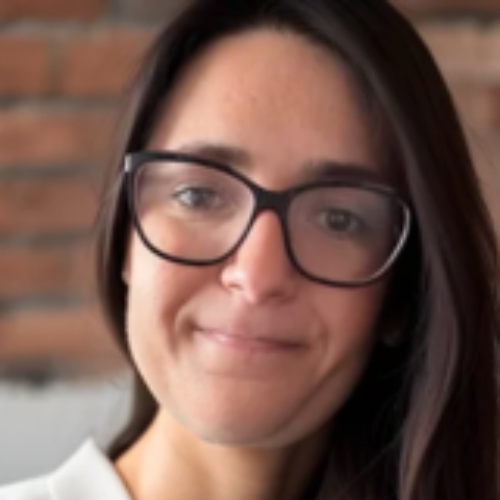
THE RESULTS
SAY HELLO TO EFFICIENT OPERATIONS
Staci USA now has comprehensive visibility into their packaging processes, which comes with near-instant troubleshooting with Rabot Pack. The Rabot system has improved employee engagement, and fostered better communications across the business, leading to greater collaboration between operational management and client engagement teams. With comprehensive coverage for all orders leaving the warehouse, Staci has been able to set a systematic baseline to continually measure and monitor packing performance to ensure efficiency and accuracy.
The days of tedious, manually built spreadsheets for quality assurance in packaging are over. Not only that, but 3PLs and warehouse and fulfillment logistics brands like Staci USA have a great need to scale in the midst of continued explosion of demand for ecommerce services and products. Rabot’s AI vision is paving the way for the future of fulfillment.
Get a Quote
Ready to get started? We are here to answer your questions